ISO 13485:2016 – MEDICAL DEVICES QUALITY MANAGEMENT SYSTEM (MDQMS)
The ISO 13485:2016 standard is an excellent way to meet all medical device quality management system standards. Adherence to ISO 13485:2016 provides a solid framework for manufacturers to satisfy Medical Device Directives, rules, and duties while demonstrating a commitment to medical device safety and quality.
What does ISO 13485:2016 stand for?
ISO 13485:2016 is the most frequently used international standard for quality management in the medical device industry. The ISO 13485:2016 standard, developed by the International Organization for Standardization (ISO), effectively meets the fundamental requirements for a QMS in the medical device business. Adopting ISO 13485:2016 gives manufacturers a realistic foundation for addressing the EU Medical Device Directive (MDD), the EU Medical Device Regulation (MDR), and other legislation, as well as demonstrating a commitment to medical device safety and quality.
DOCUMENTS REQUIRED FOR ISO 13485:2016 – MEDICAL DEVICES QUALITY MANAGEMENT SYSTEM
• Quality objectives and a quality policy.
• Medical Equipment Manual for the quality management system.
• Medical device process management must follow this procedure.
• Infrastructure and maintenance activities must meet specific requirements.
• Requirements for the workplace
• Control arrangements for tainted or possibly contaminated goods
• Risk management process in product development
• Procedures and records for medical device servicing and service validation.
• Data analysis and corrective action procedures and records
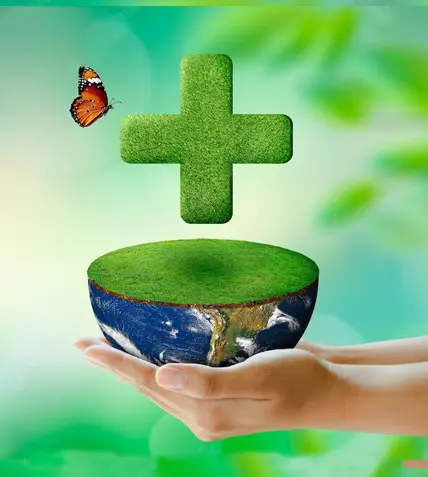
REQUIREMENTS IN GENERAL
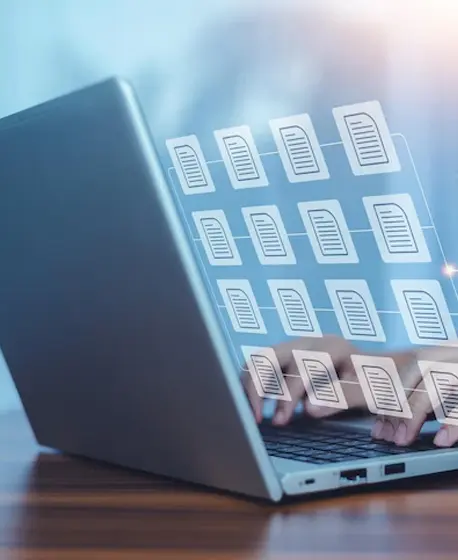
• Technical documentation (medical device file/technical product file) is provided.
• Requirements for design and development
• Implementation of a risk management process in the product development and realization process.
• Process verification.
• Requirements for health, safety, and staff cleanliness
• Change management, market research, and product recall procedures
• Observance of legal and regulatory obligations
• Product tracking and recall solutions that work.